New popular service - reconditioning of hybrid vehicle high voltage batteries
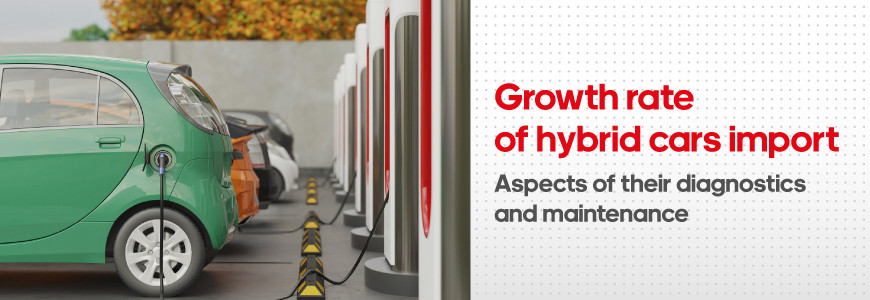
Hybrid cars were originally created as a transition to all-electric cars. With the introduction of plug-in hybrid cars to the market, their popularity has increased, as they offer significant fuel savings over traditional cars in urban areas. In addition, hybrid cars have a positive impact on the environmental friendliness of cities, so many countries economically incentivise their purchase. This fact has prompted most car manufacturers to produce hybrid versions of existing car models, for example: Mitsubishi Outlander PHEV, Ford Fusion Energi, Hyundai Ioniq, Volvo V60, Audi E-tron, Chrysler Pacifica, Range Rover PHEV and others.
Development of the range of hybrid and alternative fuel vehicles in the world
Operating a hybrid car is no more hassle for the owner than a traditional car. However, over time all owners face one problem – it is the loss of capacity of the traction battery. The traction battery – is the most stressed element of a hybrid car as it has to discharge and recharge constantly. Therefore, it is the traction battery that is – the main source of concern. As the battery ages, its capacity decreases and the cells deteriorate, and this deterioration is uneven. Critical ambient temperatures: extreme heat or extreme cold can also shorten its service life. Car manufacturers lay down the service life of the battery equal to the service life of the car, on average it is 8-10 years. With proper use and timely maintenance, batteries can last up to 15 years.
A structural disadvantage of all traction batteries is that they are subject to a cascade effect, i.e. failure of one cell leads to failure of neighbouring cells and so on. The main cause of failure – is overheating. All batteries have their own cooling system and if the car owner doesn't keep an eye on it, then battery failure is inevitable.
When a car owner experiences a significant drop in traction battery capacity or an error on the dashboard for the hybrid system, it is 90% of the time due to battery failure, and as with other units, there are three repair options: replace with a new battery, replace with a contract battery, or rebuild the battery.
When a car owner experiences a significant drop in traction battery capacity or an error on the dashboard for the hybrid system, it is 90% of the time due to battery failure.
It is quite expensive to replace a battery with a new one, but offers for contract batteries, at a much lower price, are in abundance. However, buying a contract battery involves a lot of risk, as few people can provide information about the condition of its modules. For this reason, the service of reconditioning hybrid car traction batteries is now gaining popularity.
Tractor battery diagnosis and reconditioning
It is not possible to know the condition of the battery modules by in-built diagnostic tools in cars. Currently, the only way to determine the condition of each module – is to remove the battery from the vehicle, partially disassemble it and check it with a special tester.
High-voltage battery prepared for inspection
In the MSGEquipment– line of equipment is the MS800 tester, which allows you to determine the capacity of each module of a high-voltage nickel-metal hydride battery (Ni-Mh, NiMh). The tester can test up to 36 battery modules at a time in a fully automatic, 24/7 mode. The MS800 tester has all the necessary safety features: over-polarisation protection, short-circuit protection and overheating protection. So while a battery is being tested, the technician is preparing the next battery to be tested or repairing a tested battery.
Tester MS800 in the process of checking the battery
The MS800 tester operates from 220V mains and draws 12A at maximum load. The tester has a compact size, easy-to-use touchscreen control and software upgrade capability.
The MS800 is designed to operate on 220V mains power and consumes a maximum of 12A.
Customer Economic Benefit of Battery Recovery
According to the experience of Master Service Electro, Ukraine's first specialised centre for servicing electric cars and hybrids, traction battery reconditioning is very profitable for customers. For example, let's take a case of battery restoration of a 2013 Lexus RX450h. With 10 faulty modules out of 30, the customer paid the equivalent of $750. If we compare it with the cost of a new one, it is approximately $7500, if it is a contract battery, then here the price ranges from 1500 to 3000$. Or the second example – rebuilding a 2012 Toyota Prius 30 car battery. With 2 faulty modules out of 28, the customer paid an amount equivalent to $250. The price of a new battery is about 2800$, a contract battery costs 850 – 1500$.
A new battery is about 2800$, a contract battery costs 850 – 1500$.
Conclusions
Opening a service (direction) for hybrid car battery reconditioning – is the key to the demand of the service station for many years to come. Since the global trend of the automotive industry is related to hybrid cars and electric cars. At the moment in Europe more than 24% of new cars sold, falls exactly on hybrids and electric cars. And sales have been booming in recent years.
Sales growth dynamics of the 10 most popular hybrid car models in Europe (thousand units)
The availability of MS800 tester at the service station allows not only to provide service on restoration of power batteries of hybrid cars, but also gives the opportunity to sell contract batteries, already tested and 100% serviceable, which is a significant competitive advantage in the market of second-hand spare parts. If after diagnostics of a contract battery, it turns out to be defective, it is an excellent source of spare modules for remanufactured batteries. So the MS800 tester always delivers a positive result.