A brushed motor and a brushless motor. Overview.
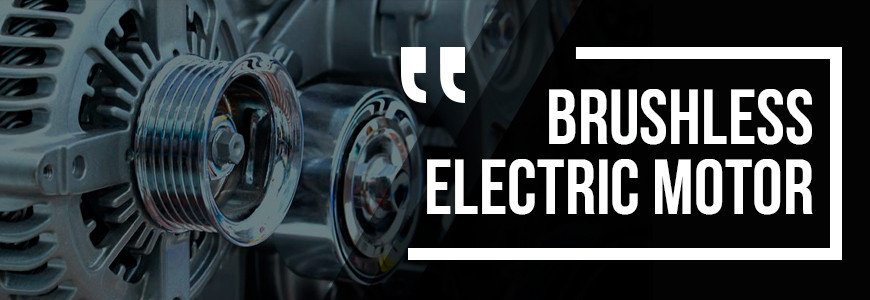
A direct current electric motor – is an electrical device that converts direct current electrical energy into mechanical energy. Virtually all direct current electric motors have an internal mechanism, either electromechanical or electrical, to periodically change the direction of current flow.
Direct current motors were the first to be widely used in the world. The speed of electric motors can be controlled over a large range by varying the voltage or by varying the current on the windings.
Brush motor
The brush motor generates torque directly from the power supplied to it, using an internal commutator, stationary magnets (permanent or electromagnetic), and rotating electromagnets.
The advantages of brush motors are: low manufacturing cost, high reliability, and easy speed control.
Disadvantages of brushed motors: high maintenance costs and short life span with high usage.
Brush motors have high maintenance costs, high reliability, and easy speed control.
Maintenance includes regular replacement of the graphite brushes as well as cleaning or replacing the commutator. These components are important for the transmission of electricity to the rotor winding.
Brushless electric motor
In a typical brushless electric motor, the rotor is in the form of permanent magnets rotating around a stator with electromagnets. The controller of such a motor converts direct current to alternating current. This type is mechanically simpler than the brushed type because it eliminates the complexity of transmitting electricity to the rotating rotor of the motor.
The motor controller can track the position of the rotor using Hall effect sensors and can control timings, phases etc. very precisely, and the current on the rotor windings can be used to optimise torque, store energy, control speed and even provide some braking.
The advantages of brushless motors are long life, no maintenance and high efficiency.
Disadvantages of brushless motors: high manufacturing cost and a more complex speed controller.
Comparison of brush and brushless electric motors
Brush electric motors were invented in the 19th century and are very common. It wasn't until the invention of semiconductors in the 1960s that brushless DC motors could be produced.
About the commutator
In brush motors, this assembly is in the form of a rotary switch on the motor shaft called a commutator. It consists of a rotating cylinder divided into n number of segments (contacts) on the rotor. These segments are connected to the rotor solenoid windings. Two or more (mostly two) stationary contacts called «brushes», made of soft (compared to commutator) conductor, make sliding contact with the segments on the commutator. With each half-turn, the commutator reverses the direction of current on the rotor windings, so that the magnetic field produces torque in only one direction.
Main disadvantages of the commutator:
- The sliding contact of the brushes with the commutator results in energy loss, which can be a significant disadvantage.
- Brushes wear due to friction, creating dust, over time brushes should be replaced.
- Sliding contact resistance causes voltage drop.
- Repeated abrupt changes in current flow through the induction of the windings cause the commutator contacts to spark and create electrical «noise», which can lead to electromagnetic interference with nearby electrical circuits.
By the way, the current flow through the induction of the windings should be changed.
Brushless electric motors were created to eliminate these drawbacks.
Brushless Solution
The development of semiconductors in electronics in the 1970s made it possible to remove the commutator and brushes in DC electric motors. In brushless electric motors, an electric servo system replaces the mechanical commutator assembly. Electrical sensors detect the angle of the rotor and control solid-state switches such as transistors, which switch current through the windings and also redirect the current (in some motors, simply switch it off) at specific times every 180 degrees. This is how electromagnets create torque in one direction. The elimination of sliding contacts in electric motors has made it possible to get rid of mechanically wearable components and add to the service life. The service life of such motors is limited only by the service life of their bearings.
That's why modern power steering systems use brushless motors in their design.